
J46-WE-8 Type Test Engine (Hagley Museum and Library)
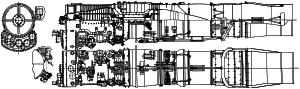
J46-WE-8B Assembly Diagram (Hagley Museum and Library)
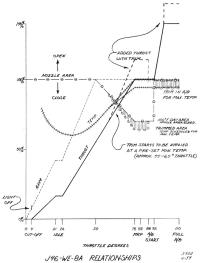
J46-WE-8A Output and Condition versus Throttle Position |
The J46-WE-8, as used in the Vought F7U-3, was an afterburning axial flow turbojet incorporating an iris-type variable area exhaust nozzle that permitted constant rpm and exhaust gas temperature in its normal operating power range. From 0° to 50 ° of throttle angle the nozzle was left open so that the engine could attain 100% rpm at a relatively low power setting (approximately 55% of Military Rated Power). As the throttle was advanced further and the fuel flow increased, the exhaust nozzle was scheduled to close in proportion to the throttle position. This nozzle closing would create a back pressure behind the turbine wheel thereby maintain the differential across the turbine wheel to hold 100% rpm, as the additional fuel was being added. Closing continued until Military Rated Power was reached. Advancing on into afterburning resulted in the rapid opening of the nozzle and an increase in thrust to 140%. The rpm of the engine remained at 100% from 50° of throttle on to full afterburning.
Through use of an automatic temperature control unit the exhaust nozzle was caused to close an additional amount, which maintained an optimum exhaust gas temperature and a resulting higher thrust. Maximum permissible exhaust gas temperature was maintained at both Military and afterburning with a proportional amount being obtained below Military and as dictated by throttle position.
The J46-WE-8A engine developed a sea level static thrust of 3,905 lbT (Military) and was augmented with afterburning to produce 5,500 lbT The J46-WE-8B engine produced 3,980 lbT in Military and 5,800 lbT in afterburner. Normal Rated Power (maximum continuous) was approximately 90% of Military or basic engine and was obtained at approx. 93.5% of the maximum permissible operating temperature.
Maximum engine rpm was 10,100 with an idle of 44% ±4%. When developing rated thrust the engine consumes 74 lb of air per second. The basic engine (military power) fuel consumption was approximately 11 gals per minute and while in afterburner the figure was more than 2.5 times as much. The engine was designed to use JP-4 (MIL-F-56240) but was also operated on 115/145 grade aviation gasoline following certain adjustments. Maximum permissible operating temperature was in the 700°C range with the exact limit for each engine being determined at the factory and documented in its logbook. Engine life was 150 hours of all condition time although time was logged separately under total time, military time and afterburning. All time above 93.5% of the maximum permissible operating temperature was logged as Military time and was limited to 30 minutes of operation. Afterburning time was likewise logged separately but its time limitation would vary with altitude due to a F7U airframe fuel feed problem. There was no restriction on ground runs except those which may be imposed due to the noise level. The afterburner was good as long as it remained serviceable.
Engine Dimensions
Length with Afterburner = 200 inches
Diameter = 29 inches
Vertical Height = 37.3 inches
Horizontal Width = 31.6 inches
The power plant assembly weighed approximately 2,000 lb with 242 lb added for the quick engine change unit.
This article was made possible by Al Casby, who generously lent his rare F7U-3 Service Training Manual for scanning, and to Paul Christiansen, who provided the scanned images to the AEHS. This material was used for Paul's new book, Westinghouse J46 Axial Turbojet Family, which is reviewed elsewhere on this web site.
|