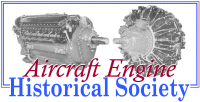 |
enginehistory.org Aircraft Engine Historical Society Members' Bulletin Board
|
View previous topic :: View next topic |
Author |
Message |
tfey
Joined: 13 Jul 2003 Posts: 104 Location: Arlington Hts., IL
|
Posted: Sat Nov 27, 2010 18:04 Post subject: Franklin progress and pics |
|
|
The engine exterior has been cleaned up and now resides in my basement. The two magnetos I received with the project have been professionally hybridized to a single working unit (engine is a single ignition system) through the skill and generosity of an A&P AEHS member. I opened the sump to poke around, found a little sludge but no corrosion or suspended metal. The oil pump lookd fantastic. I cleaned the oil pump intake screen and trunk. Took a while to clean the nasty old gaskets off the crankcase and sump cover, but got it done. A trip to the auto parts store for some gasket material and the hardware store for some .032 stainless steel wire to use as safety wire made for a fun afternoon cutting and punching gaskets aas well as my first foray into safety wiring. I laminated a 2 x4 with some 1/4 inch plywood, then drilled a 2 inch hole for the prop shaft, two 3/8 inch diamter bolt holes, and a hole for a crank handle so that sooner or later I can turn the enging over to pump some oil through her and see the mag make sparks. I also bought a $16 (non-electric) oil pressure gauge at the auto parts store for eventual use in the control panel
Hopefully the link will get you to some of the pics of the project.
http://www.enginehistory.org/BBimages/tfey/
and
http://www.enginehistory.org/BBimages/tfey/EisemannAM4Magneto/index.html |
|
Back to top |
|
 |
tfey
Joined: 13 Jul 2003 Posts: 104 Location: Arlington Hts., IL
|
Posted: Sun Nov 28, 2010 09:01 Post subject: |
|
|
The bolt and compressor blade in the picture deck are some things I picked up in trade. The compressor blade is from the 9th stage of a J58 as used on the SR-71 Blackbird. The bolt is a 3/4 diameter titaninium bolt that weighs only 4 ounces also from the Blackbird. Both artifacts are true works of art. |
|
Back to top |
|
 |
rwahlgren
Joined: 15 Aug 2003 Posts: 324
|
Posted: Tue Dec 07, 2010 01:52 Post subject: |
|
|
Great pictures. Looks like it was well protected from corrosion.
Thanks for sharing. |
|
Back to top |
|
 |
tfey
Joined: 13 Jul 2003 Posts: 104 Location: Arlington Hts., IL
|
Posted: Tue Dec 07, 2010 20:10 Post subject: Franklin |
|
|
Still making slow progress. I got the sump cover and oil pump cleaned, re-gasketed, and buttoned up. I made a crank stooge for the prop shaft. I'm going to put a few quarts of straight mineral based oil in her and hand crank it until I hopefully see oil weeping out of the rocker arm pivots and rod big ends. First oil through it in maybe 60 years. If not, well, then I've got a bit of more work to do. Still cutting new gaskets for the rocker boxes and top crankcase cover. Check back now and then for more pics. |
|
Back to top |
|
 |
tfey
Joined: 13 Jul 2003 Posts: 104 Location: Arlington Hts., IL
|
Posted: Sun Dec 12, 2010 17:41 Post subject: |
|
|
Unable to wait any longer, I bought some SAE 30, non-detergent mineral oil from Ace Hardware, filled the sump, took the rocker covers off, removed the plugs, shot some oil onto the cylinders from the crankcase and a little through the spark plug holes, oiled the wrist pins and valve guides, then turned the crank. Lucky me, oil flowed nicely to all four cylinder heads despite my anemic 30 second duration, 50 rpm pace. The crankshaft was very quickly coated with oil and I could hear the big end oil jets spitting at the cylinders every once in a while if I cranked hard enough. The exhaust rockers have holes drilled in their tips to shoot oil to the valve stems, and all four flowed very well. I did notice that the intake rocker on #1 didn't have oil dripping from it like the rest, so I took that out, cleaned it up, and oil drips from it now. I had to grind a 1/2 inch sockets down to make it thin wall so I could get it on to the rocker shaft bolts which are quite close to the rocker arm itself. I have not hooked up the oil pressure gauge, but doubt I could get much pressure at 50 rpm. The oil remained quite clear with very little contamination with old oil coming through the lines.
Next job is to set the valve lash, clean and paint the rocker covers, cut some new gaskets, then reattach the covers for good. Toughest part will be trying to paint in the house or my unheated garage without fuming the family or making the 10 o’clock news here in Chicago.
New pics have been posted at the link above. |
|
Back to top |
|
 |
tfey
Joined: 13 Jul 2003 Posts: 104 Location: Arlington Hts., IL
|
Posted: Wed Dec 22, 2010 23:49 Post subject: |
|
|
I have already cleaned up the sump, oil intake oil intake screen, and oil pump. I cut a new gasket, painted the sump cover, and the sump is now all closed up. I found a little sludge, but not bad, and the aluminum oil pump seemed to be in great shape. Magneto has been completed by an A&P.
Unable to wait any longer, I bought some SAE 30, non-detergent mineral oil from Ace Hardware, filled the sump, took the rocker covers off, removed the plugs, shot some oil onto the cylinders from the crankcase and a little through the spark plug holes, oiled the wrist pins and valve guides, then turned the crank. Lucky me, oil flowed nicely to all four cylinder heads despite my anemic 30 second duration, 50 rpm pace. The crankshaft was very quickly coated with oil and I could hear the jets spitting at the cylinders every once in a while if I cranked hard enough. The exhaust rockers have holes drilled in their tips to shoot oil to the valve stems, and all four flowed very well. I did notice that the intake rocker on #1 didn't have oil dripping from it like the rest, so I took that out, cleaned it up, and oil drips from it now. I had to grind a 1/2 inch sockets down to make it thin wall so I could get it on to the rocker shaft bolts which are quite close to the rocker arm itself. It seems the left side rocker boxes get more oil flow (measured by drippage into the pans) than the right side, but all seem to get plenty even at low rpm. I have not hooked up the pressure gauge, but doubt I could get much pressure at 50 rpm. The oil remained quite clear with very little contamination with old oil coming through the lines.
Next steps are to complete the valve lash adjustments, cut some gaskets, paint the rocker covers, and seal up the rocker boxes for good. Then I start work on the carburetor, which appears to be no more complicated than my lawnmower. Perfect!
So I was adjusting the valve lash and found that I could not compress the #4 intake lifter down to allow adjustment to 0.04 in. (1 mm) valve lash. I also noticed the lip of the pushrod cup rode right up against the bottom of the rocker arm and the ball was not doing the bearing work in the cup. Uh oh. So then I loosened up the intake rocker shaft bolts, hoping that the intake valve will close tight. Then I turned the crank and found very little compression in cylinder #4 (finger over the plug hole test). More uh oh. Other cylinders seem to have good compression. This meant to me the jug had to come off, so I took the plunge.
The exhaust valve is the smaller, cleaner valve while the intake is the larger diameter, sooty valve. It looks like the intake valve is not seating down as far as maybe it should, maybe a result of it not closing completely due to the lifter problem. The engine must have been running for a while like this because the underside of the rocker has a small arc that has been smoothed by the pushrod lip. So I figure I need to lap the intake valve into shape. Once the valve is out I'll be able see how it is seating. I also need to replace or repair the hydraulic lifter, and that I have to look into. I also need to buy a ring compressor, but I'm getting ahead of myself.
I tested the valve seal by dumping gas in the cylinder, and lo and behold, the exhaust valve leaked a little while the intake held dry! Go figure. I was betting on the intake as the leaker. So I removed the valves, which was quite a bit of fun, using the tricks Kim suggested. The valve springs for the intake valve had two U-section base washers and a shim on the bottom, so they may have been shimmed up to make up for weakness at some point.
I also disassembed the two lifters, which twist apart into 2 pieces. They looked pretty clean, but I blew them out with carb cleaner, then let them sit in penetrating oil anyway. They both now behave similarly under compression and release from compression. So I think they are ready to go.
The intake valve has a nice, even, shiny mating surface on it. The exhaust valve has a similar mating mark, but is much less shiny. Not sure if that is normal or not. I plan to lap both valves to their seats to visualize and hopefully improve their seal. Seats look OK as far as I can tell. Valves were straight and true by rolling stems on glass table.
The adventure continues. |
|
Back to top |
|
 |
tfey
Joined: 13 Jul 2003 Posts: 104 Location: Arlington Hts., IL
|
Posted: Sun Dec 26, 2010 23:54 Post subject: |
|
|
I got my Flex-hone in the mail and put it to work. I bought the 3.75 inch, 240 grit model, ran it all oiled up at 700 rpm in a portable drill and made maybe 5 passes total. The surface lookes pretty good to me and I didn't want to take much metal off. There is a small ridge at BDC, but I have no interest in boring, oversize pistons, new rings etc. I cleaned the cylinder in soapy water, dried it up, and re-installed the valves. The cylinder now liquid-tight by the gasoline-in-cylinder test. Tomorrow I paint it up a little and reinstall the jug. Then the compression test. That will decide whether I yank the other 3 cylinders.
I checked the valve guides for wear by measuring how much the partially open, springless valves deflect under side load on the end of the stem, then a load in the opposite direction. The good news was a total deflection of 0.002 inches, which is under the limit. Which is fantastic because no way am I changing valve guides.
More pics soon. |
|
Back to top |
|
 |
tfey
Joined: 13 Jul 2003 Posts: 104 Location: Arlington Hts., IL
|
Posted: Fri Dec 31, 2010 09:07 Post subject: |
|
|
Well, the piston entry into the cylinder went quite easy. But when I was installing the cylinder the intake trunk apparently hung up on the internal metal lip that retains the intake pipe seal which resulted in sharp metallic pop and a broken aluminum elbow casting. The flange tang that has one of the two bolt holes sheared at the pipe edge. Not happy.
I had lightly greased the intake and pushrod tubes with silicone grease to help ease them into their seals, but the intake tube hanging up on the lip was an unpleasant surprise. I had backed off the intake studs to allow some movement of the intake trunk but was starting to bear down on the base studs when it broke. All my fault.
The internet yellow pages listed several aluminum welders in my area. I picked a guy who has been doing mobile welding out of his truck for 25 years. Turns out he does a lot of work on old engines. He doesn't think repairing the flange will be a big deal, but cautioned that old castings sometime give trouble. My casting is 72 years old. I'll get it back sometime next week.
Note to self: If it takes more force than can be overcome with 3 fingers on your weaker hand, STOP. Something is amiss. |
|
Back to top |
|
 |
|
|
You cannot post new topics in this forum You cannot reply to topics in this forum You cannot edit your posts in this forum You cannot delete your posts in this forum You cannot vote in polls in this forum
|
Powered by phpBB © 2001, 2005 phpBB Group
|