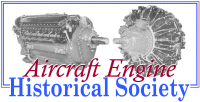 |
enginehistory.org Aircraft Engine Historical Society Members' Bulletin Board
|
View previous topic :: View next topic |
Author |
Message |
mhamer
Joined: 19 Apr 2013 Posts: 17
|
Posted: Wed Jan 23, 2019 08:12 Post subject: R2800 CB16 Valve setting PWA 5654 depressor needed |
|
|
i have been restoring a R-2800 for a running display.
it's now time to set the valves. The book says to release 2 valves and adjust 2 at a time. (i can't because i have only 1 depressor pwa5654)
in this video he uses only 1 depressor and calls for 20 in/lbs to set the opposite valve. is this an accurate method? 20 in/lbs doesn't account much for variations in the drag of the screw threads, and friction on the contact point..
i prefer the 2 released valve method per the book.
Wanted 1 PWA 5654 vale depressor
https://www.youtube.com/watch?v=4fBmpM0kWd8
Thanks |
|
Back to top |
|
 |
kmccutcheon

Joined: 13 Jul 2003 Posts: 299 Location: Huntsville, Alabama USA
|
Posted: Wed Jan 23, 2019 12:15 Post subject: Re: R2800 CB16 Valve setting PWA 5654 depressor needed |
|
|
I don't understand why you need more than one tool. Other books tell you to do what the Precision Engines video says, or give the option to do either. You don't need any particular accuracy because the 20 lb-in torque value is intended to be strictly a limiting torque so you don't apply more force to the push rod, cam follower and cam ring than is required to seat the cam ring against its spigot before beginning adjustment of the other valve on that cylinder. _________________ Kimble D. McCutcheon |
|
Back to top |
|
 |
mhamer
Joined: 19 Apr 2013 Posts: 17
|
Posted: Wed Jan 23, 2019 16:39 Post subject: |
|
|
Thanks. So it’s ok with 20 in/lbs even if the screw is stuck ? |
|
Back to top |
|
 |
kmccutcheon

Joined: 13 Jul 2003 Posts: 299 Location: Huntsville, Alabama USA
|
Posted: Wed Jan 23, 2019 17:07 Post subject: |
|
|
NO. Free the screw by chasing the threads in the 'nut' or filing the threads on the screw with a thread file, then proceed with the procedure. The screw needs to be finger-loose in the tool. _________________ Kimble D. McCutcheon |
|
Back to top |
|
 |
mhamer
Joined: 19 Apr 2013 Posts: 17
|
Posted: Thu Jan 24, 2019 15:59 Post subject: |
|
|
20 in/lbs on a fine thread screw won’t apply the same pressure as 20 in/lbs on a coarse thread screw. It’s dependant on tpi, size of screw and distance to the pivot point. I still prefer the old method you release 2 and adjust 2. Therefore the need for another depressor. PWA 5654 |
|
Back to top |
|
 |
rwahlgren
Joined: 15 Aug 2003 Posts: 324
|
Posted: Sat Feb 09, 2019 21:56 Post subject: |
|
|
It is more accurate to use the Jim Lewis method. Both methods will work, since the shop manual method was used for a long time. The problem I see is using the 2 levers and then release, it runs the chance of moving the cam ring a smidge. With 2 people it might be better, again adjusting per that video is a better method. Oh and that video method is so much easier, no charts to figure out which valves to depress etc. less chance of error. Jim is no longer at Precision, and Precision no longer does radial engine overhauls, just fuel system stuff and some PMA as well.
And on some display unit, if your used to twisting wrenches you don't need to worry about 20 in lbs, you just snug and feel the slack being removed, on the very first adjustment just snug the lash adjust screw into the valve spring a small amount, I'm sure there is a lot of valve to piston clearance and your not going to go crazy cranking pressure on the valve spring so all should be good.
Edit here. Using either method especially my loading a valve spring, a bore scope to check for sure any valve to piston clearance, and also an indicator to prove the play or clearance is removed from the valve train, as the 20 in lbs or what ever is used to take the slack out, the lack of indicator movement would confirm it. Though an over tight condition would show movement because you could introduce stretch, just remember 20 in lbs is not very tight at all. A small 1/4 drive ratchet using one hand and not over doing it will accomplish what is needed. |
|
Back to top |
|
 |
|
|
You cannot post new topics in this forum You cannot reply to topics in this forum You cannot edit your posts in this forum You cannot delete your posts in this forum You cannot vote in polls in this forum
|
Powered by phpBB © 2001, 2005 phpBB Group
|