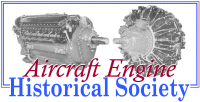 |
enginehistory.org Aircraft Engine Historical Society Members' Bulletin Board
|
View previous topic :: View next topic |
Author |
Message |
tfey
Joined: 13 Jul 2003 Posts: 104 Location: Arlington Hts., IL
|
Posted: Sun Feb 06, 2011 14:19 Post subject: Franklin Restoration Feb. 2011 |
|
|
Finally got the crankcase cover and the 4 valve covers painted. Quite a pain in frigid Chicago without a heated a garage. An attic ventilation fan blowing vertically out of my basement window well witht the front door cracked open and the heat off did the job for painting. A bathroom with a ventilation fan did the job for extended drying. I have a very patient wife; fume tolerant, too.
The original paint job was black with the raised "Franklin" lettering sanded to show the aluminum surface. I decided to paint the lettering with a light ivory color as white was too stark and silver too boring. Looks old school. Scrapeing the old gasket material off the mating surfaces was tedious, but tedious is what it took. Cutting new gaskest was simple.
As for how and if to paint the rest of the engine will be a Springtime endeavor. I may just sand down the external edges of the cooling fins to show the aluminum and hand-paint the pushrod tubes, intake trunks, and crankcase. The exhaust manifolds are hefty sand-cast aluminum with some finning, so I may sand the edges smooth and polish them up.
Engine is finally sealed up, the Marvel-Schebler MA-8F is next. I'll be shopping for trailers in early Spring.
Tom |
|
Back to top |
|
 |
dirwin
Joined: 21 Aug 2010 Posts: 13 Location: West Sussex, England.
|
Posted: Sun Feb 06, 2011 17:27 Post subject: |
|
|
Tom,
Any photos during the work and the final result?
Thanks,
DAI |
|
Back to top |
|
 |
tfey
Joined: 13 Jul 2003 Posts: 104 Location: Arlington Hts., IL
|
|
Back to top |
|
 |
rkammlott
Joined: 26 Jul 2004 Posts: 47 Location: Teaneck NJ
|
Posted: Mon Feb 07, 2011 15:14 Post subject: |
|
|
looking good Tom! |
|
Back to top |
|
 |
tfey
Joined: 13 Jul 2003 Posts: 104 Location: Arlington Hts., IL
|
Posted: Sun Feb 20, 2011 20:37 Post subject: |
|
|
Refurbishing the carburetor:
Luckily for me, the Marvel-Schebler MA3 is a very simple carb; 2 main pieces, no accelerator pump, altitude compensation, or pressure anything. There's a diagram of the carb and pics of the carb parts in the picture section. My refurbishment of the carb and indeed the engine are to my (basement) standards: good and safe ground operation, decent looks, with affordable functionality, and not necessarily to manufacturer overhaul specs, museum display or airworthy status. I’m a backyard mechanic, not an A&P, and parts are very hard and expensive to come by. Plus this engine will run, but never fly. But the hardware , prop, and mount will be aircraft quality.
The carb has an idling circuit which shunts the fuel+air mixture up a metered tube to a port that exits into the carb bore on the engine side of the mostly-closed butterfly. A needle valve allows adjustment of the idle mixture. The idling circuit is on the left hand of the diagram and is self-activated by the high suction created on the engine-side of the butterfly. When the butterfly is mostly closed the main nozzle has very little suction across it and contributes very little to fueling the engine.
The main circuit has a brass power jet that meters fuel into a tubular chamber where the brass main nozzle mixes fuel with metered air to feed the main nozzle bore that projects into the center of the venture. The introduction of air into the fuel stream before it hits the venturi provides better mixing and vaporization of the fuel. Instead of an intact stream of fluid coming out the idling or main nozzle (like an open garden hose), a mist comes out, something like your kitchen water faucet with an aeration screen. The main nozzle comes on line when the airflow and suction is increased as the butterfly opens and engine speed increases.
The cast aluminum carb top and lower bowl are held together with 4 screws. The carb was amazingly clean inside; long empty of fuel, but no varnish or gum. I removed the jets, fuel screen, inner venturi assembly, etc., soaked them in a glass jar with 50% gasoline and 50% carb cleaner in my garage for a day or two, then blew them clean with carb cleaner. I examined the bores and metering holes under magnification with good light, backlight via flashlight, and found them clean and smooth. I removed the float to check the fuel float valve and valve seat and found them to be clean and smooth, so back on went the float with a new cotter pin to secure the float hinge shaft. A check of the floats found them both to be at the correct height off the carb deck as per the manual.
I choose not to take off the butterfly as I found no significant wear or play in the shaft and didn't want to tempt fate with taking it apart and busting something for little gain. The ends of the 2 screws that hold the circular butterfly plate onto the throttle shaft are squeezed to compress the end threads to prevent loosening, backing out, and the engine ingesting a screw. This operation is best accomplished with a specialized squeezer which I don't have, so after cleaning with WD-40 (miraculous stuff for cleaning) followed by carb cleaner, I oiled the shaft bearings and that was good enough.
The disassembled carb was washed and scrubbed in Simple Green degreaser with a nylon brush and green scotchbrite cloth. Light sanding with 320 paper improved the surface, but I did not sand or strip the paint down to bare aluminum. Any place that was gummy got additional cleaning with WD-40 followed by degreaser. All passages were shot clean with a final jet of carb cleaner and checked a final time for cleanliness.
After wiping the parts clean with solvent, I painted the carb halves by brush with gloss black Rustoleum enamel in my ventilated bathroom (I live outside Chicago and it's cold in February), let it sit a day to dry, and baked it to final drynesss at 170 degrees for an hour in our kitchen oven. The raised lettering was painted with light ivory model enamel.
The various parts were screwed back into place and a new paper gasket was made from auto part store gasket sheet with scissors, Exacto knife, and hole punches. The carb went back together in 20 minutes with another 20 minutes for safety wiring.
Maybe more than you want to know, but if you lived next door, I’d have made you come over and look……. |
|
Back to top |
|
 |
tfey
Joined: 13 Jul 2003 Posts: 104 Location: Arlington Hts., IL
|
Posted: Sun Feb 27, 2011 20:00 Post subject: |
|
|
I spent some time this weekend fitting up the prop. The propeller is a 44 inch diameter 4-ply laminated wood unit, model 22008, made by US Propellers. As far as I can find out, these were used on a variety of drones from the 1940’s on out to maybe the 1960’s. My best guess is that this prop, which has crush marks, was run on a McCullough 2 stroke engine anywhere from 65 to 75 horsepower at up to 4200 rpm. The Franklin made 50 hp at 2300 rpm when brand new, so this prop should be plenty sturdy for my use. It has a fairly aggressive pitch, so it remains to be seen if the Franklin can achieve full rpm with this unit. The modest prop diameter means the engine mounting on the trailer can be relatively low compared to the height that a standard, $2000, 70 inch diameter prop would require.
The prop has 5/16 diameter bolt holes, suitable for AN5 bolts, but the Franklin prop flange has 3/8 diameter bolt holes. Unwilling to irreversibly alter the prop and possibly weaken it as well, Kim McCutcheon came through by machining some top hat-type adapters to neck down the bolt holes and provide a bearing surface on the back of the prop flange for the washer and castellated nut. Kim also machined the 5 inch diameter aluminum crush plate for me. As the pictures show (see link above), all the pieces went together beautifully. With the bolts snug, but not yet tightened to running torque, there is about 2 mm clearance between the back of the prop bolts and the crankcase. Thanks, Kim!
The prop needs a little cosmetic clean up, but that will have to wait for the warmth of Spring. Next jobs are to get the engine mount blasted clean so I can inspect it before painting, and spend some time wet sanding and polishing up the aluminum exhaust stacks. They are pretty rough castings, but maybe the ribbing and top can be smoothed and polished to add a little shine to the project. Plug wires also need to be fabricated. |
|
Back to top |
|
 |
tfey
Joined: 13 Jul 2003 Posts: 104 Location: Arlington Hts., IL
|
Posted: Tue Mar 01, 2011 22:45 Post subject: |
|
|
I put the magneto on just for kicks today (no spark plugs, plug wires, or fuel) and was moving the prop slightly to fool with the prop bolts when the impulse coupling on the magneto snapped loudly as it is supposed to. I felt the click right through the prop. The last time I heard an unexpected metallic ping the intake flange cracked. Scared the willy out of me until I realized it was a good sign. |
|
Back to top |
|
 |
|
|
You cannot post new topics in this forum You cannot reply to topics in this forum You cannot edit your posts in this forum You cannot delete your posts in this forum You cannot vote in polls in this forum
|
Powered by phpBB © 2001, 2005 phpBB Group
|