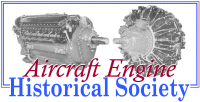 |
enginehistory.org Aircraft Engine Historical Society Members' Bulletin Board
|
View previous topic :: View next topic |
Author |
Message |
sbezman
Joined: 13 Jul 2003 Posts: 12
|
Posted: Tue May 03, 2005 07:45 Post subject: TSIO-520-VB failure |
|
|
The NTSB recently posted AAR-04-03 on its web site concerning the failure of this type engine. I found the maintenance aspects interesting, and thought others might like to read it. www.ntsb.gov |
|
Back to top |
|
 |
kmccutcheon

Joined: 13 Jul 2003 Posts: 299 Location: Huntsville, Alabama USA
|
Posted: Wed May 04, 2005 07:29 Post subject: |
|
|
Very interesting reading indeed! I think the thing that surprised me most about the accident report was my lack of surprise at most of the findings. The quality of equipment, maintenance, personnel, recordkeeping and procedures are probably typical of the low-end of the PART 135 spectrum. However, three things really raised my eyebrows: The extreme engine TBO extension; the six-phase progressive inspection; and the use of unapproved lubricants during engine assembly.
TBO extension: I cannot fathom how anyone thought a 50% extension of the manufacturer’s recommended time-between-overhaul period was a good idea. PART 135 operators are not required to follow manufacturer’s recommendations, but the ones I am familiar with usually do. Any other action typically requires a long and involved justification process, so it us almost always simpler to just write the PART 135 Manual to embrace manufacturer’s recommendations.
Progressive Inspection Schedule: The result of the six-phase inspection schedule was to extend the time between engine compression checks from the customary 100 hours to almost FOUR TIMES that long (360 hours), which, in my opinion, is entirely too long. A more frequent inspection interval might have detected a loose or missing cylinder base nut and prevented the accident.
Unapproved Lubricants: Aircraft engine manufacturers specify the sealants, lubricants, other materials, along with associated processes, that are acceptable for use during overhaul and maintenance. In each case, there is substantial test data supporting the use of these specific materials and processes. ANY substitution of materials and processes for those recommended by the manufacturer requires an equivalent testing process to assure the new material or process is equivalent to the old. Here we see that something as simple as using an anti-seize compound in place of the recommended assembly oil can be catastrophic. Unfortunately, I suspect that such substitutions are far more common that we would like to believe. _________________ Kimble D. McCutcheon |
|
Back to top |
|
 |
sbezman
Joined: 13 Jul 2003 Posts: 12
|
Posted: Thu May 05, 2005 03:51 Post subject: |
|
|
Thank you for your comments. Similar thoughts occurred to me. I also was surprised that the people doing the differential compression checks did not seem very familiar with the specific requirements for the procedure or the engine health information this test can provide when properly done. It is dissappointing that individuals responsible for safety of flight sometimes lose sight of how critical their actions are. Conversely, it is inspiring to consider how many individuals are dedicated to safety of flight and it these individuals who keep the whole thing together. |
|
Back to top |
|
 |
|
|
You cannot post new topics in this forum You cannot reply to topics in this forum You cannot edit your posts in this forum You cannot delete your posts in this forum You cannot vote in polls in this forum
|
Powered by phpBB © 2001, 2005 phpBB Group
|