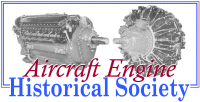 |
enginehistory.org Aircraft Engine Historical Society Members' Bulletin Board
|
Critical Information |
|
You have been banned from this forum. Please contact the webmaster or board administrator for more information. |
|
|
Powered by phpBB © 2001, 2005 phpBB Group
|