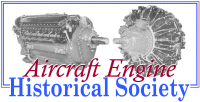 |
enginehistory.org Aircraft Engine Historical Society Members' Bulletin Board
|
View previous topic :: View next topic |
Author |
Message |
dpennings
Joined: 10 Dec 2016 Posts: 48
|
Posted: Mon Feb 22, 2021 13:52 Post subject: engine oil in high flying planes |
|
|
Hi everyone,
I asked this question in the "oil in sump during operation" thread, but didn’t get an answer, maybe nobody read this
So, I start another try, how did they prevent oil evaporation when flying extremely high? Had the crank cases been pressurized, or were the oil temperatures super low, or did they use special oils which enable high flying?
Dominik |
|
Back to top |
|
 |
rwahlgren
Joined: 15 Aug 2003 Posts: 324
|
Posted: Wed Feb 24, 2021 18:18 Post subject: |
|
|
I don't have my manuals handy here and will study it a bit later and modify this post when I have more information.
(In response to a pressurized crankcase.)
First of all in any fuel burning 4 stroke, reciprocating piston engine the bad stuff has to be vented or purged from the crankcase, if it isn't massive amounts of sludge would occur as well as acid build up in the lubricant and other impurity's. Then you have to think about the oil dilution systems that purposely pump raw gasoline into the engine oil to reduce the viscosity for the next cold start. That gasoline is suppose to disappear from the oil as it heats up to operating temperature, to return that oil back to its normal viscosity. Those vapors have to go someplace. On a C-97 Engine QEC there is a tube sticking out of the left side behind the engine, into the air stream, that is the crankcase (accessory case) vent. I say it is similar to the road draft tube of the old early 50's cars and trucks that I remember, though it isn't as oily and dirty. PCV wasn't used in the old days, especially not on aircraft. Lets also not forget about blow-by. Evaporation at high altitudes? It was more of a consumption and leaking problem, and is why a system for adding extra oil to the engines was installed on the KC and C -97's, also most large engine installations used in large propliners, have very large quantity oil tanks for reasons mentioned as well as for any evaporation losses. As a wild guess without doing the experiment I think the heavy viscosity of 120 aviation engine oil that is equivalent to SAE 60, would have very little evaporative loss, and not a huge concern. A quick search found nothing on the Noack of aviation engine oil.
If a crankcase is pressurized, that would help over come the oil control rings (force oil past them), strain the oil seals at shafting exposed to low atmospheric pressures at altitude, add more windage losses, and give blowby gases, and water vapor no place to go, unless a heavy system was added to recycle the the crankcase (internal engine) air, and that was designed to separate out and remove the nasty destructive vapors, and retain pressure in a crankcase. All of course adding more weight, adding more cost, taking up more space, all for something that would cause more problems than it would help.
In automotive racing a negative pressure is what they desire in the crankcase, do you know why?
Read the Noack and how the test is done.
http://www.pqiamerica.com/June%202014/consolidated%200W-20.html
Mass % loss, 1 hour @ 250 degrees C. ASTM 5800
250C = 482F from an online calculator. That is some warm oil, and is why aircraft engines have oil coolers.
This fellow on youtube is great. This test shows some evaporative loss.
https://www.youtube.com/watch?v=OUSKxOPTzzc |
|
Back to top |
|
 |
avasko
Joined: 13 Jul 2003 Posts: 37 Location: Ft Collins, CO USA
|
Posted: Sun May 02, 2021 19:06 Post subject: Oil Evaporation |
|
|
Excellent reply above. Then too, 50 weight oil, even when hot is not exactly volatile. The engine itself burned oil and, for example, the radar Connies (WV-2/EC-121) had two 67 gallon auxiliary oil tanks to replenish engine oil 40+ gallon tanks in flight s as the engines consumed it. I doubt very little was lost to "evaporation". The engine breathers could expel a lot of oil particularly if the scavenge pumps weren't working very well, sometimes due to clogged screens or as I saw once, a failed hydraulic pump shaft seal pushed about 15 gallons of the red mineral fluid into the engine rear case. Breathers really did a job of coating the wings that time.
And then to, engines like the BA series R3350 leaked a lot too. In fact a clean BA engine was a sign of an fuel injection line leak. |
|
Back to top |
|
 |
|
|
You cannot post new topics in this forum You cannot reply to topics in this forum You cannot edit your posts in this forum You cannot delete your posts in this forum You cannot vote in polls in this forum
|
Powered by phpBB © 2001, 2005 phpBB Group
|