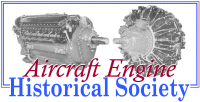 |
enginehistory.org Aircraft Engine Historical Society Members' Bulletin Board
|
View previous topic :: View next topic |
Author |
Message |
aburhoe Guest
|
Posted: Thu Nov 26, 2009 14:16 Post subject: heat rejection rates |
|
|
Can anybody provide me with heat rejection rates for any of the water cooled V12 engines? I’m particularly interested in racing applications, but would also like to see data on these engines used in “normal” service.
Actual flow rates and delta T across the radiator would be best, but I’ll settle for BTU per minute if it’s derived from hard data.
Thanks in advance!
Aaron Burhoe |
|
Back to top |
|
 |
rwahlgren
Joined: 15 Aug 2003 Posts: 324
|
Posted: Thu Apr 22, 2010 21:07 Post subject: |
|
|
I read that specific heat rejection rates were in the 15 BTU/Min/BHP,
less than 10% of fuel energy to cooling. For some liquid cooled WWII aircraft engines. No specifics though, like power settings etc.
You see alot of information about liquid cooling offering more power because of greater heat rejection on the net. I would think the opposite.
That is the reason for cummins experimenting with its Adiabatic Diesel Engine in the 70's. Heat rejection means lost energy. Its best to use all the heat you can, and why the Turbocyclone was getting the excellent fuel consumption numbers it did.
Yes low heat rejection in a gasoline engine means more susceptibility to detonation, and thus loss of power, and possible failure.
The biggest advantage of liquid cooling is better control of the engine temperature. It is much more difficult to control cylinder and head temperatures in an aircooled engine, especially something like the Wasp Major. Sorry to get off topic. |
|
Back to top |
|
 |
dpennings
Joined: 10 Dec 2016 Posts: 48
|
Posted: Wed Feb 07, 2018 13:14 Post subject: |
|
|
It sounds like a good idea to isolate the combustion chamber walls, but in most cases, it won’t help to reduce heat losses. Air offers good isolation and heat losses in a combustion engine are already quite low. You should note, that most of the heat losses take place during the exhaust stroke. Tests with adiabatic engines mostly resulted in lower efficiency due to increased heat losses (sic!). If the wall temperature is above 300°C, the fuels burns directly at the wall, thus giving very high heat losses during combustion. In conventional engines, there is no combustion directly at the wall and thin layer of air is giving quite a lot of isolation.
Most air cooled engines needed very rich mixtures at full power to keep the temperature down, whereas liquid cooled engines are less prone to overheating.
The best way to reduce heat losses during combustion are: large cylinders, long stroke, high supercharging, small compression ratio. Besides that, a short exhaust port with small surface (e.g. by using only one exhaust valve) is also very effective to reduce heat losses but it will not increase engine effectivity a lot. |
|
Back to top |
|
 |
sdavies
Joined: 14 Jul 2019 Posts: 2
|
Posted: Wed Jul 17, 2019 08:27 Post subject: Re: heat rejection rates |
|
|
aburhoe wrote: | Can anybody provide me with heat rejection rates for any of the water cooled V12 engines? I�m particularly interested in racing applications, but would also like to see data on these engines used in �normal� service.
Actual flow rates and delta T across the radiator would be best, but I�ll settle for BTU per minute if it�s derived from hard data.
Thanks in advance!
Aaron Burhoe |
I have seen heat flow diagrams from RR, Allison, P&W and Wright. (Probably required for some government contract?) They are all very similar! Less than 25-30% goes to the prop, ALL of the rest is lost and rejected, one way or another. Engine exhaust, oil coolers, engine radiators, coolant and oil pumps, oops, forgot the fuel pump and supercharger drive too. All of these things soak up energy that could be driving the prop if the engine truly was adiabatic, SP?
I assume, there's that word again, that trying to figure out how much heat is lost to any one system is very time consuming and difficult given the paucity of similar reports from other sources. Maybe it is something they foist off on college students for semester projects? While the Mustang's radiator installation is the best in the world, the stock set up can not get rid of as much waist heat as the supped up engine makes and they are required to resort to all kinds of gimmicks and spray bars in a vain effort to get rid of excess heat.
During every race, the guys driving air cooled engines must wait till they reach race temp before they can open the throttle WFO. On the other hand the LC engine guys must carefully modulate their throttle poss during the race, or wait and save their throttle till the end to prevent over heating the engine. It's a sort of hair and the tortoise game. The LC guys jump to an early lead and the AC guys hope the can over haul the leaders before the end of the race. |
|
Back to top |
|
 |
|
|
You cannot post new topics in this forum You cannot reply to topics in this forum You cannot edit your posts in this forum You cannot delete your posts in this forum You cannot vote in polls in this forum
|
Powered by phpBB © 2001, 2005 phpBB Group
|